Alright, let’s talk about something that popped into my head the other day – Dave Bristol. Not the guy himself, well, sort of about him, but more about a simple thing he showed me years back that I ended up re-doing in my own garage just last weekend.
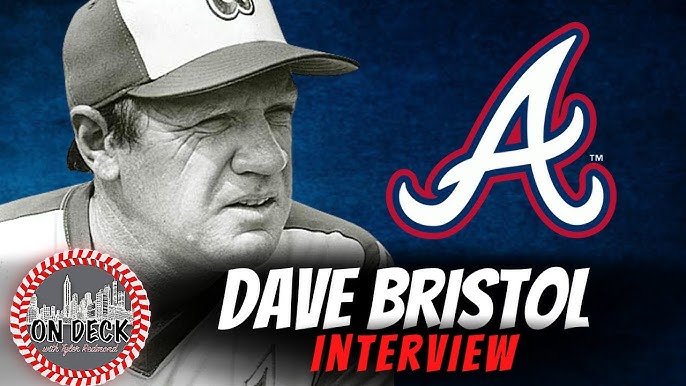
So, picture this: my workbench was a total disaster zone. Again. You know how it gets. Tools piled up, screws mixed in with bolts, couldn’t find the pliers when I needed ’em. Standard stuff. I was getting pretty fed up trying to get anything done.
Remembering Dave’s Way
Then I remembered Dave Bristol. Used to work with him way back. Quiet guy, but his workspace? Always spotless. Not like fancy spotless, just… organized. Everything had its place. One afternoon, I was hunting for a specific wrench in the shared shop, grumbling as usual, and he just kinda pointed to his little setup.
He didn’t make a big deal out of it. No fancy systems. What I noticed was how he used simple stuff, like old jars and basic racks, but everything was grouped by use. Not just type, but what you’d likely need together for a job. Seemed obvious, but seeing it laid out made a difference.
What I picked up from him was basically this:
- Group tools by the kind of job you do most often.
- Use clear containers if you can, so you see what’s inside. Jars, old plastic tubs, whatever.
- Put the stuff you use all the time right where you can grab it. Don’t hide it.
- Things you use rarely? Put ’em away, but label where they are.
Putting it into Practice (Again)
So, last Saturday, I decided enough was enough. I pulled everything off my workbench. Everything. Spread it out on the floor. It was a mess, honestly took longer than I thought.
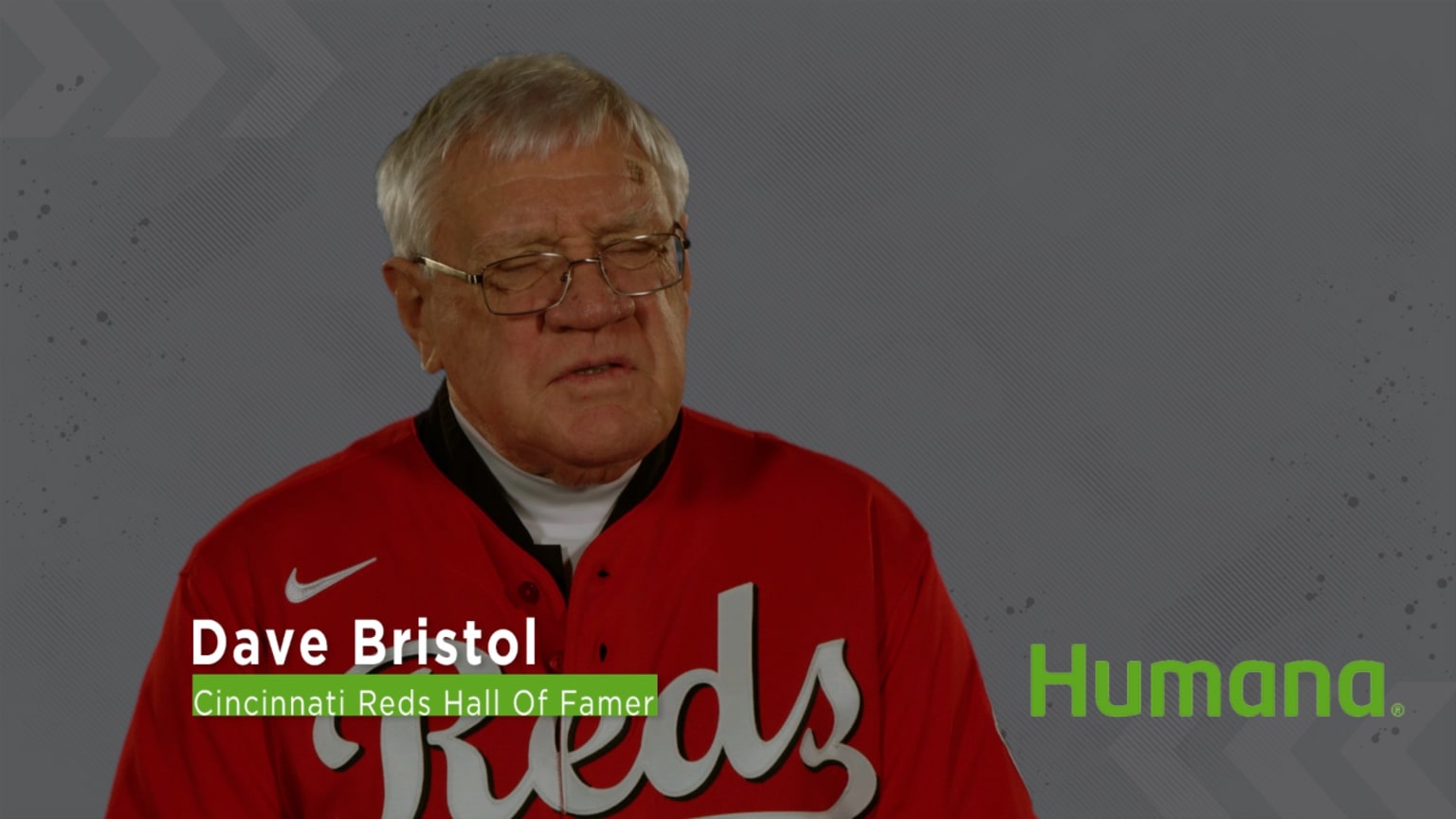
First, I just sorted into big piles: screwdrivers here, wrenches there, electrical stuff, cutting tools, you get the idea. Then I started thinking like Dave. Okay, when I fix the lawnmower, what do I always need? Socket set, specific screwdrivers, spark plug wrench. Okay, that’s one group. Basic plumbing leak? Pipe wrench, plumber’s tape, adjustable wrench. That’s another group.
I found a bunch of old coffee cans and those clear plastic containers my wife saves. Cleaned ’em out. Started loading them up based on those ‘job groups’. Got some pegboard hooks I had lying around and put the most-used hand tools right above the bench, easy to grab.
It wasn’t rocket science. It took a few hours, mostly sorting and figuring out the best layout for me. Had to move things around a couple of times before it felt right.
Now? It’s way better. I actually finished a small project yesterday without spending ten minutes looking for the right size Philips head. It just feels less chaotic. It’s funny how those simple lessons, like the ones you pick up from guys like Dave Bristol just by watching them work, stick with you and actually make a difference down the line. Just gotta remember to actually do them.